WHY PISTONS AREN’T ROUND
To the untrained eye, the skirt of a piston would appear to be perfectly cylindrical. To be fair, even to the trained eye that would seem to be the case. But if you were to roll a piston on its side down a flat slope, you’d notice that it gradually wanders off path – that’s because the shape of the skirt isn’t round! In this technical blog we uncover what shape it actually is, and why.
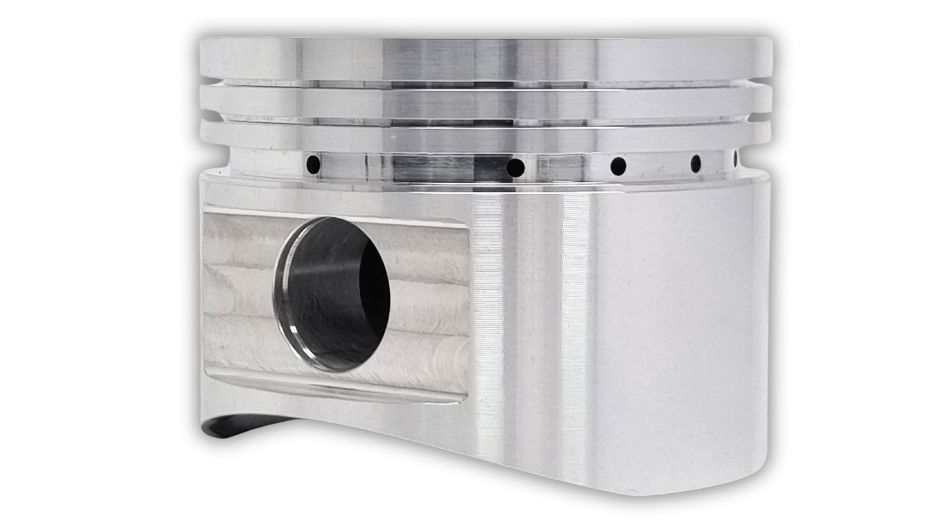
Looking at the piston side on, the profile of the skirt is actually barreled, not straight. And looking from the top, the shape of the piston is oval, not circular. Actually, you’d be hard pressed to notice this by eye, as we are talking in terms of fractions of a millimeter, but its enough to make a difference when the piston is running in an engine.
This barreling and ovality is intentional – it’s there to take account of the deformation of the piston when it is loaded up and heated up, which has the potential to result in inconsistent bore clearance and possible seizure.
Bore Clearance
The clearance between the skirt and the cylinder bore’s inner diameter is critical, for many reasons. Too much clearance will allow the piston to tilt in the manner described above, whereas insufficient clearance can result in catastrophic seizure. Note also that tilting the piston can lead to increased movement of the rings and more wear of the ring grooves.
Generally, the running clearance is dictated for full-load operating conditions. The clearance is influenced by engine speed and piston temperature, so other operating conditions may also need to be considered. For example, the piston temperature and hence expansion can increase during lean running, which can lead to an unforeseen reduction in clearance.
Note that the recommended bore clearance is also affected by the materials of the piston, cylinder liner (if present) and cylinder block, specifically with regards to dissimilar thermal expansion rates. Even the two grades of the most prolific aluminium alloys in use these days – 2618 and 4032 – have different thermal expansion rates that mean the bore clearance needs to be different for each alloy.
Normally a piston made from a 2618 alloy will require more bore clearance than one made from a 4032 alloy. That isn’t an issue during running, as once the pistons have reached their operating temperatures the chosen bore clearances will be the same for both alloys, but it can cause a problem on start-up or when cold as the extra clearance required for the 2618 piston can create more noise.
Piston Skirt Loads
In a conventional reciprocating four-stroke engine the small end of the con rod will articulate forwards and backwards around the gudgeon pin as the crankshaft completes one revolution. As a result, the piston will be subjected to side loads that vary for each of the four piston strokes.
The largest side load by far will be during the power stroke, when a combination of inertia and gas loads will push the piston sideways as well as downwards. This is commonly referred to as the major thrust side load, and its direction is always on the side that is against the direction of rotation.
For example, if the crankshaft rotates clockwise when viewed from the front then the major thrust side will be on the left-hand side. The opposite side of the piston is referred to as the minor thrust side, and the minor thrust side is subjected to a lower sideways force during some of the other stages of the four-stroke cycle.
As well as deforming the shape of the piston, these major and minor side loads can have an extremely detrimental effect on the operation of the piston. For example, they can promote tilting or rocking of the piston in the bore, which can exasperate wear at the top of the lands and at the bottom of the skirt. This type of movement can also create vibrations that are then radiated through the engine and can even be detected and heard outside the engine, commonly called piston slap.
Piston Skirt Deformation
The external loads imparted to the piston from the gas pressure in the combustion chamber above the piston are immense, and will cause strain deformation of the piston shape and in particular the piston skirt area. The resultant shape of the skirt after this deformation is a complex one.
During the firing cycle the crown will be deformed inwards by the loads from the gas pressure in the combustion chamber, effectively splaying the skirt outwards. If the piston were shaped like a cup then the skirt deformation would be circular, but of course the piston incorporates the pin boss and structural ribs, so the deformation isn’t even.
The pin bosses provide support along the pin axis, so the skirt deformation at the piston’s open end can be broadly described as oval, with the diameter increasing along the pin axis and decreasing at the major and minor thrust directions. The shape isn’t completely elliptical though, as there are additional strain deformations in the skirt to consider. The pin bores themselves are subject to loads from the gudgeon pin, which can effectively flatten the skirt, and the skirt itself is deformed by the contact pressure acting on the skirt from the cylinder bore.
Superimposed on top of these strain deformations is the effect of thermal expansion. The temperature is highest at the crown, so at working temperature the diameter around the crown and around the lands will expand outwards more than the diameter of the skirt.
There will also be a gradual reduction in diametric expansion down the length of the skirt, decreasing as one goes down the skirt away from the crown. Like the strain deformation, the thermal expansion of the skirt isn’t even due to the presence of the pin bosses and structural ribs.
When the strain deformation and thermal expansion of the piston are combined, the resulting skirt topography ends up being a combination of broadly oval sections that increase and decrease in size down the length of the skirt, following what is best termed a barrel profile. Note that some manufactures refer to the barreling as cam or curvature.
Now, if one assumes that the bore in the cylinder block or cylinder liner is perfectly cylindrical during running (which it isn’t) then the shape of the piston skirt’s profile when it is machined has to be carefully designed so that it deforms (both by strain deformation and thermal expansion in the manner described above) when running to create a complementary perfect cylinder. As a result, piston designers will have to specify the necessary ovality and barreling of the skirt and lands that the machinist will need to achieve at room temperature.
Piston Skirt Design
When designing a piston, special attention is paid to the topography of the skirt. The shape of the skirt can have a large influence on engine performance, as it can control the tilting of the piston, lateral displacement, oil film thickness and frictional losses. As mentioned, the shape of the skirt is defined by barreling and ovality.
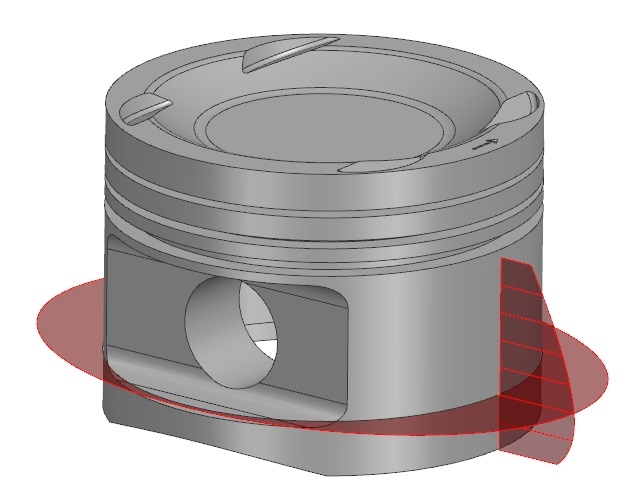
The simplest design of piston skirt will have the same amount of ovality along the entire length of the piston, and in some cases this will suffice. The designer ensures that the area of the skirt that will have the largest amount of expansion is catered for, but the remaining sections of the skirt will have a looser fit during running than might be desired, which can cause problems with reduced stability of the rings and poor guidance of the piston in the bore.
Going one step further to solve these issues, the ovality at staged sections down the length of the piston can be prescribed as a series of ellipses, which in turn are defined by their major and minor diameters, and which change in size following a barrel form. Commonly, this is done at discrete points roughly every 1-2 mm down the length of the piston.
The derivation of these ovalities would traditionally have been found from trial and error, requiring a series of engine tests to monitor the condition of the skirt. The pistons could only be inspected by removing them, hence such testing would require a number of rebuilds.
Too much contact between the skirt and the wall of the bore would be indicated by scuffing, which would indicate the areas that needed to be addressed. In the worst case, overly excessive contact would cause a catastrophic seizure, making it impossible to inspect the running surfaces left in the piston debris.
With the advent of FEA (finite element analysis), piston designers can calculate the combination of strain deformations and thermal expansion to derive the required skirt profile. Load cases for various stages in the operating cycle and different running conditions can now be considered to optimise a single profile for a number of scenarios. In addition, the piston designer can now take into account the effect of bore distortion.
The assumption that the bore is perfectly cylindrical during engine running isn’t necessarily true, even if the bore has been honed at temperature and with torque plates fitted to simulate distortion from the assembly and running loads induced by the cylinder heads, sump or mains caps, and crankshaft mains journals. There will still be some distortion to this circular section, which normally corresponds to the locations of the studs or fasteners next to the bore.
FEA can be a very powerful tool to predict the actual shape of the cylinder bore, and the results from it can be used to define the required piston skirt profile. Piston designers are turning to increasingly intricate computer-derived simulations, creating complex dynamic multi-body simulations based on the structural and thermal FEA of the piston and bore. The results of this analysis can create skirts that have the optimum contact conditions for a wide range of operating conditions.
So, the first objective of a good skirt design is to ensure that there is the correct clearance between all the parts of the lands and load bearing area of the skirt and the wall of the cylinder bore. As we’ve already seen, there are a number of factors that can influence bore clearance, and the chosen profile must take into account each of these factors.
Nowadays though, designers are also considering the dynamic behaviour of the oil that is trapped between the skirt and the bore. There has been plenty of published research into the effects of piston skirt profile on the lubrication of the piston and its subsequent influence on friction.
Such research concludes that the frictional behaviour of the piston is heavily influenced by the mode of lubrication (hydrodynamic, mixed and boundary), which in turn is constantly changing throughout the four-stroke cycle owing to the reciprocating motion of the piston. Further, it has been noted that almost 80% of the frictional power loss from the skirt occurs during the power stroke.
Piston Skirt Machining
The required shape of the skirt by the designer can be machined by mounting the piston on a rotating spindle, which is then moved in and out of a rotating grinding wheel whose movement is controlled by an eccentric cam. Manufacturers use specialist CNC piston turning centres for this, and they can be programmed by entering the required diameters and ovalities at the discrete sections down the length of the piston, as defined by the designer. Note that this type of machining will extend up above the skirt to the lands, and can include the ring grooves themselves.
More advanced machining centres now use modern diamond turning instead of grinding to achieve a tighter tolerance on the skirt profile. Some machines will need to be temperature controlled or will have an element of temperature compensation built into them to eliminate the potential problem of thermal expansion during machining – even a shift of 10 oC above room temperature can push the profile out of tolerance. In addition, as design techniques have advanced over the years the required profiles have become more complex.
As a result, skirt machining has had to be developed to allow for more complicated designs, such as the need for asymmetric skirts and even concave reverse-profile barrelling in certain sections of the piston. (On a piston with asymmetric skirts the bearing area of the major skirt is designed to be able to withstand the higher loads from the major thrust side, and as the deformation of the skirt is partly linked to side loading, it also means the skirt profile can end up being different on the major and minor skirts.)
Skirt Coatings
In theory, if the skirt profile has been designed correctly, and there is an adequate supply of oil, then there shouldn’t be any contact between the skirt and the bore, as there will always be a film of oil separating them. In reality though, that isn’t always the case – cold starts, oil contamination, overheating, extended high-speed running and many other problematic running conditions can lead to a breakdown of this hydrodynamic oil film.
Several piston manufacturers therefore apply a coating of some sort on their piston skirts, to allow the piston to survive the occasional skirt-to-bore contact. Although the major source of friction will come from the rings, there is some frictional saving that can be made with skirt coatings, and there is plenty of evidence to show that the application of coatings has helped with the durability of both the piston skirt and the cylinder bore surfaces.
Some manufacturers apply a dry-film lubricant that can be sprayed on after the skirt has been machined. For example, some of our Cosworth pistons have a fluoropolymer coating that has the tradename Xylan.
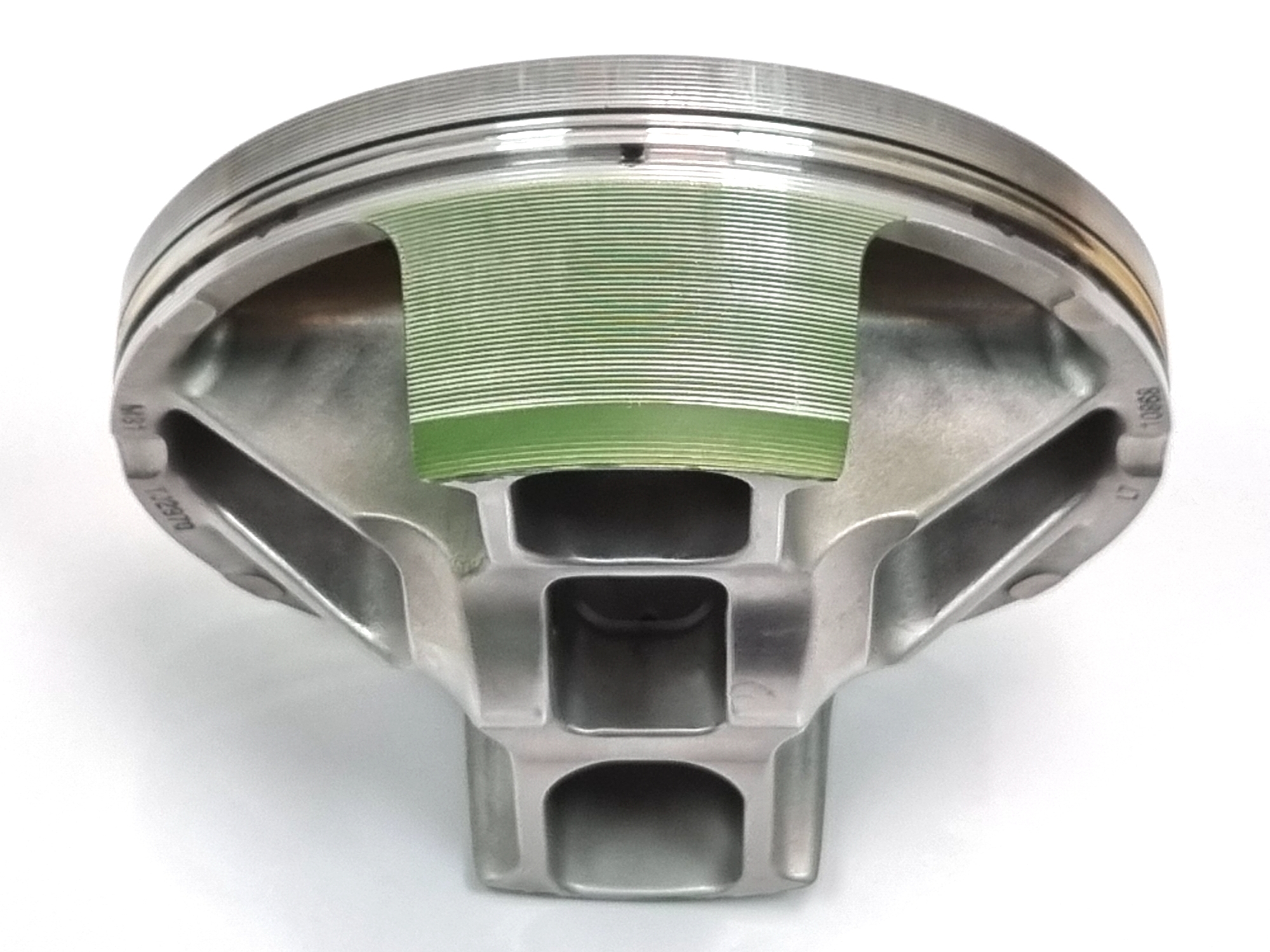
The thickness of the coating on the skirt can be quite thin, in the region of between 8 and 13 microns, and with such thin coatings there doesn’t need to be a manufacturing allowance when machining the skirt, as this coating is intended to wear (as is the case on the Cosworth TJ Formula 1 piston pictured above). Sacrificial coatings like these can also be extremely useful in identifying areas of high wear on the skirt – as long as the engine is stopped before metal-to-metal contact occurs!
This feature on pistons is based on an article written by Modatek’s Matt Grant for Race Engine Technology, issue 111. You can purchase a back copy of this publication here: https://www.highpowermedia.com/Product/race-engine-technology-issue-111