TIMING BELT TECH
One of the most important aspects of any IC engine is the correct timing of the rotational movement of the camshafts relative to the reciprocating movement of the pistons. Any errors in this timing will result in detrimental performance, and could in the worst case lead to contact between the valves and pistons, which could prove to be both catastrophic and costly. There are a number of ways that this meticulously choreographed movement of valves can be achieved, such as with gears or chains. But one of the most common methods in a road car is with the use of a timing (or cam drive) belt. The timing belt is normally driven by the crankshaft, and then turns pulleys that drive the camshafts.
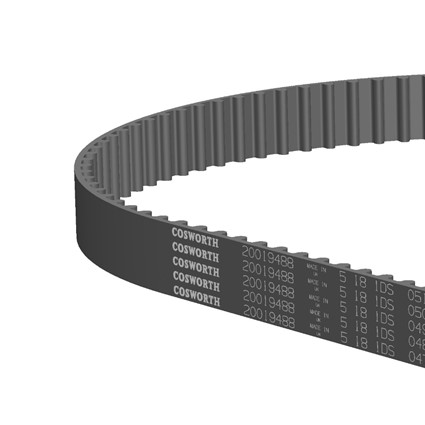
Timing Belt Construction
The majority of automotive timing belts are constructed from an elastomer body that contains tension cords, with a fabric backing and a tooth jacket.
Looking at these four ingredients one by one, then the first is the elastomer body. This is normally a high temperature spec rubber such as HNBR (hydrogenated nitrile butadiene rubber) or EPD (ethylene propylene diene). HNBR is more suited to engines, as it can handle exposure to lubricating oils. The elastomer body can sometimes be reinforced with aramid fibres, which help strengthen the belt and provide extra protection for the teeth. Aramid is a heat-resistant and strong synthetic fibre that is sometimes referred to by the tradename Kevlar. Our heavy duty belts for the YB engine contain this aramid reinforcement, which helps make them three times stronger than a conventional automotive timing belt.
The tension cords help to give the belt incredible levels of tensile strength without compromising on flexibility. Tension cords are typically manufactured from high-strength glass fibre, and the individual strands of fibre are bundled together and twisted for added strength. It is the presence of glass fibre that means that a timing belt should never be ‘crimped’, which is the action of over-bending or twisting the belt that then shears the glass fibres.
Next up we have the tooth jacket, which is a temperature-resistant polymide fabric that helps to protect the teeth from abrasion as well as shear forces. The last ingredient is the fabric backing, which is usually another type of polymide fabric. This fabric backing is used on the smooth face of the belt that will run against the belt tensioner, so resistance to abrasion and wear is a must for the fabric.

Toothed Belts
In the majority of cases the timing belt is driven by teeth on the belt that engage with matching teeth in the pulleys on the crankshaft and camshafts. It is these teeth that provide the accuracy in timing, and hence toothed belt drives are often terms ‘synchronous belts’, as the keep the movement of the cams in synch with the crankshaft.
Keeping the teeth engaged at all times is vital. If a tooth jumps out of position then this is called ‘ratcheting’ (some people might use stronger language when this happens!). It is normal for the belt teeth to try to escape from the adjacent teeth in the pulley – when this happens the belt tension increases, which pushes the teeth back together, but this can lead to long lasting damage of the tension cords inside the belt. Complete slippage of the belt teeth out of the pulley teeth usually happens because either the tooth engagement is poor, or because of lack of belt tension.
The profile of the teeth is an important factor for the performance of the timing belt, and there are generally three categories for the profile – trapezoidal, curvilinear or modified curvilinear. Curvilinear profiled belts are sometimes called High Torque Drive (HTD), and modified curvilinear profiled belts are often called Super Torque Drive (STD), S-type Tooth Profile Dual-sided (STPD) or GT.
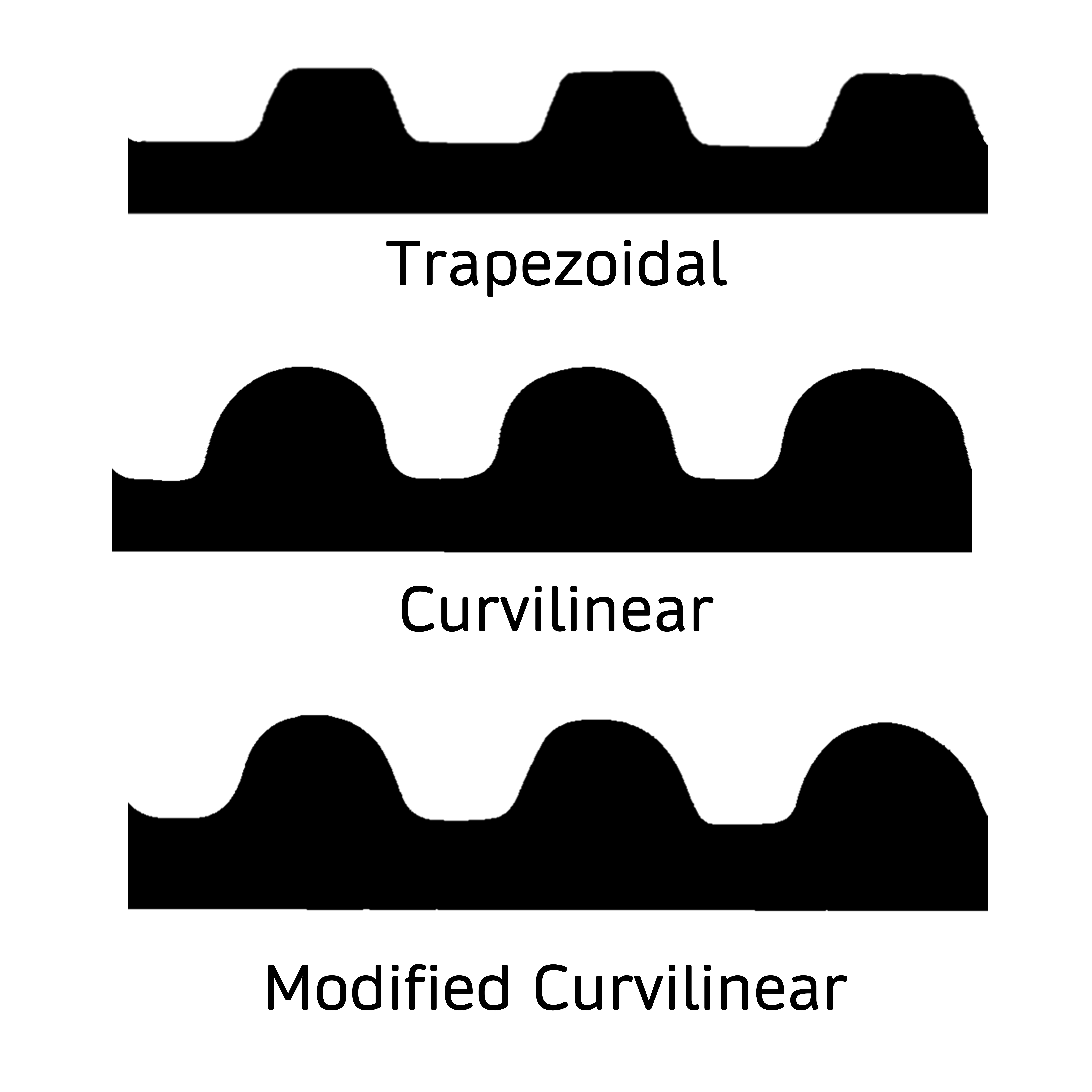
Tooth Profiles
The trapezoidal profile is the oldest of the three, introduced over 80 years ago. The shape of the profile is a trapezium, with straight flanks that are angled inwards towards the tip of the tooth. When the teeth revolve around the pulley, these flanks create an involute curve that matches the involute tooth profile on the pulley.
One disadvantage with the trapezoidal tool profile is that it has sharp corners at the root of the tooth, and this can create high stress concentrations that can weaken the belt. To overcome this, the curvilinear has fully radiused corners, which helps to even out the stresses. Also, the curvilinear tooth profile is taller than the trapezoidal profile, making it more difficult for the teeth to jump out of position and also giving a larger contact area, which in turn helps to reduce both stress and noise.
The last of these three profiles, modified curvilinear, is today the most popular type with timing belt manufacturers. As the name suggests, this profile is based on the curvilinear profile, but has a shallower tooth height along with an increase in flank angle. These changes help to give the modified curvilinear profile the ability to withstand higher amounts of torque.
Cosworth Engine Belts
Want more information on the belts that we stock for Cosworth engines? Then get in touch via our contacts page.