SUSTAINABLE FUELS & LUBRICANTS
Back in July last year, a 1972 McLaren M19 circulated around a very wet Silverstone circuit. This might not seem so remarkable, except for the fact that this represented a significant milestone for the future of historic motorsport. Why? Because the Cosworth DFV engine in the McLaren was being fed with fully synthetic petrol, a sustainable fuel from Zero Petroleum that promises to be the replacement for fossil fuels in the years to come. But what are sustainable fuels and lubricants, and why are they so important?
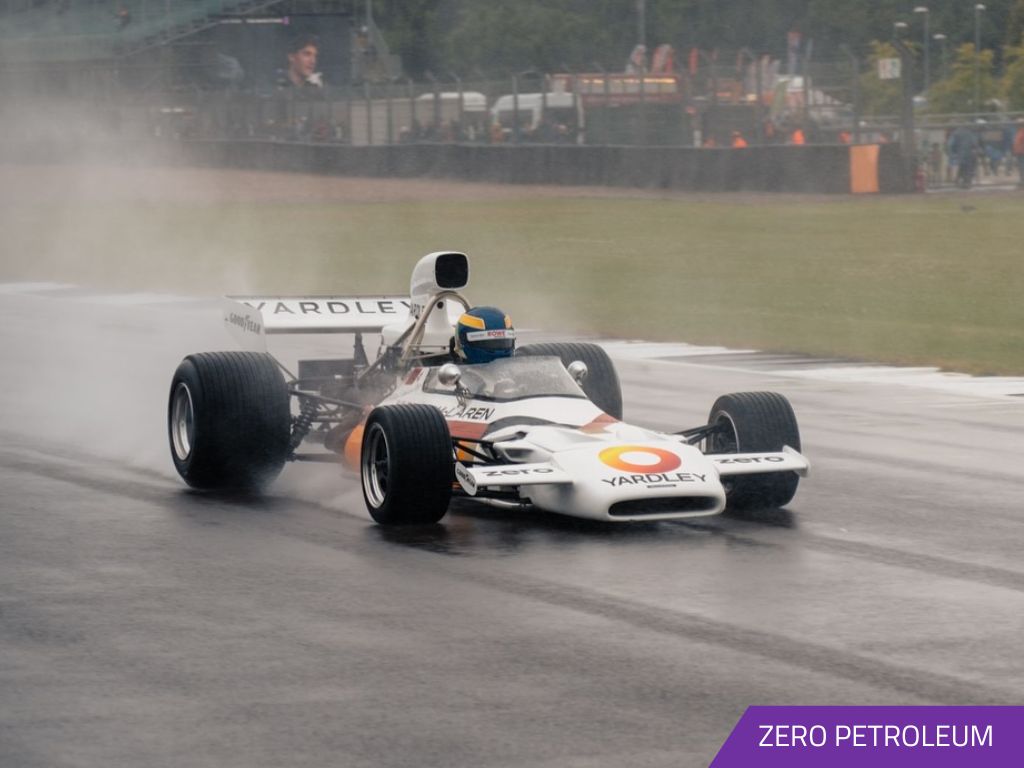
Sustainable synthetic and bio-synthetic fuels and lubricants could be the solution to the growing need to decarbonise motorsport. They are one of a number of different tactics that we can employ today to reduce carbon emissions. And unlike other methods such as electrification or switching to hydrogen fuels, the use of sustainable fuels and oils requires virtually no modifications to existing IC (internal combustion) engines.
Indeed, as part of the FIA’s desire to become ‘carbon net zero’ by 2030, a number of its top tier categories have already started to mandate the use of these sustainable fuels. WRC switched over to 100% sustainable fuel in 2022, and Formula Two and Formula Three began to ramp up the percentage of sustainable fuel used in their cars in 2023. But perhaps the most noticeable move to sustainable fuel will be when Formula 1 switches over in 2026.
In the world of historic motorsport, the use of these sustainable fuels will become even more necessary if we want to continue to use the existing IC engines that the historic cars are famous for. Who would want to contemplate replacing the iconic Cosworth DFV in the aforementioned McLaren M19 with a battery pack, inverter and electric motor, for example?
A couple of years ago I wrote an article for Race Engine Technology that looked at how these sustainable fuels and lubricants are manufactured (1). Without wanting to sound arrogant, I’ve written dozens of articles for this publication but this was in my mind probably the most important subject that I’d tackled in my 10 years of writing.
There is so much misunderstanding and misinformation in the media today about decarbonising vehicles that I thought it would be interesting to write a blog post about sustainable fuels and lubricants, and with kind permission from Race Engine Technology, I’ve been able to reuse some of the original article.
Why Do We Need Sustainable Fuels & Lubricants?
When it comes to rising carbon levels in the atmosphere, it is usually the IC engine that is maligned and not the fossil fuels themselves.
I spoke with Rebecca Mann of Coryton, who are already supplying sustainable fuel into main stream motorsport. “All too often, we demonise the IC engine,” says Mann, “but it’s the fossil fuels we put in them that cause the environmental problems. And, if we want to look at the actual environmental impact that we are making we really need to look at the bigger picture. The life cycles of the vehicle and fuel runs from its production to its disposal, and the various stages involved in this cycle can also include the creation of pollutants.
“If we want to weigh up what’s best for our planet, we need to explore the environmental impact of all these stages. Making the most of our existing vehicles whilst we develop wider solutions, such as EV, really could make a big difference.
“What’s more, sustainable fuel is ready to hit the ground running using our existing infrastructure. This means we can continue to utilise the existing fleet that we have on roads, along with the existing refuelling infrastructure.”
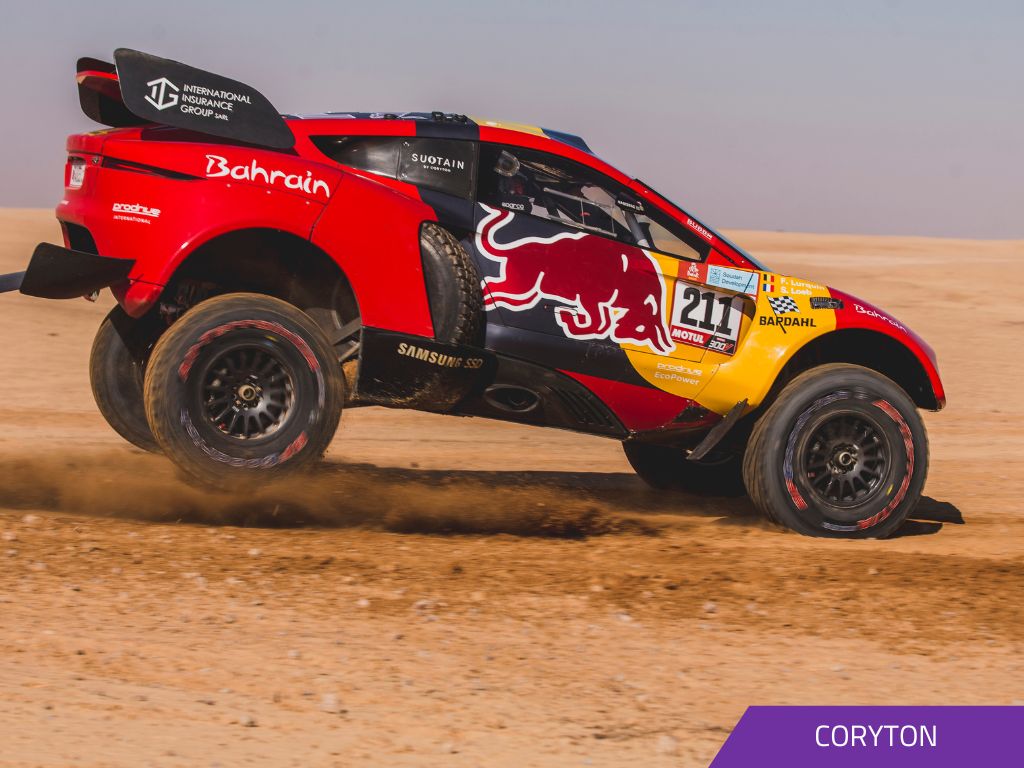
There are numerous arguments for and against the transition to sustainable fuels and lubricants, but probably one of the biggest advantages lie in the shear volume of IC engines that are in use on today’s roads.
“There are 36 million existing cars on the UK’s roads”, continues Mann, “and only 0.5% of which are currently fully electric. And there are 275 million passenger vehicles in Europe. We would rather be making moves to immediately improve these vehicles, rather than just waiting for the entire fleet to be replaced with electric vehicles or other new technologies.
“According to the UK government’s own statistics, sustainable fuel could reduce emissions by up to 80% compared to fossil fuels. Even a staged introduction could remove 130 million tonnes of carbon dioxide in Europe by 2030 – almost the same amount as 33 coal fired power stations would produce in a year.
“And, given sustainable fuel could be introduced much more rapidly than the transition to all-electric vehicles, we believe this is something we should be looking at very seriously to help tackle the climate emergency, whilst the infrastructure for electrification is put in place.”
But just how are sustainable fuels better for the environment than fossil fuels? “Sustainable fuel works by, effectively, recycling carbon,” answers Mann. “The carbon that a sustainable fuel contains is captured or absorbed from the atmosphere during the production process – for example, the agricultural products absorb carbon dioxide whilst they grow.
“Once it is turned into fuel and burnt, that same carbon is then released back into the atmosphere. Fossil fuel, on the other hand, has held its carbon safe for millions of years. Burning it releases additional carbon dioxide into the atmosphere that was not there before.”
There are two different ways to make sustainable fuels and lubricants. Bio-synthetic fuels and lubricants are processed from organic material, whilst synthetic fuels and lubricants are created by a number of chemical processes that use the existing carbon dioxide in the atmosphere. Both categories have their own advantages and drawbacks, such as cost and difficulty. Some fuel and lubricant manufacturers combine both bio-synthetic and synthetic products, whilst others continue to use fossil fuels or oils that are mixed with these sustainable fuels and lubricants.
What are Biofuels?
Bio-synthetic fuels, sometimes referred to as biofuels, and lubricants are manufactured by processing biomass – biomass is term for an organic material such as crops (like corn, soybeans and sugar cane), algae or microbial culture. These organic materials use photosynthesis to capture the carbon dioxide in the air. Burning bio-synthetic fuels is carbon-neutral, as the carbon dioxide that is produced from combustion is balanced out by the carbon dioxide that is required to produce the fuel.
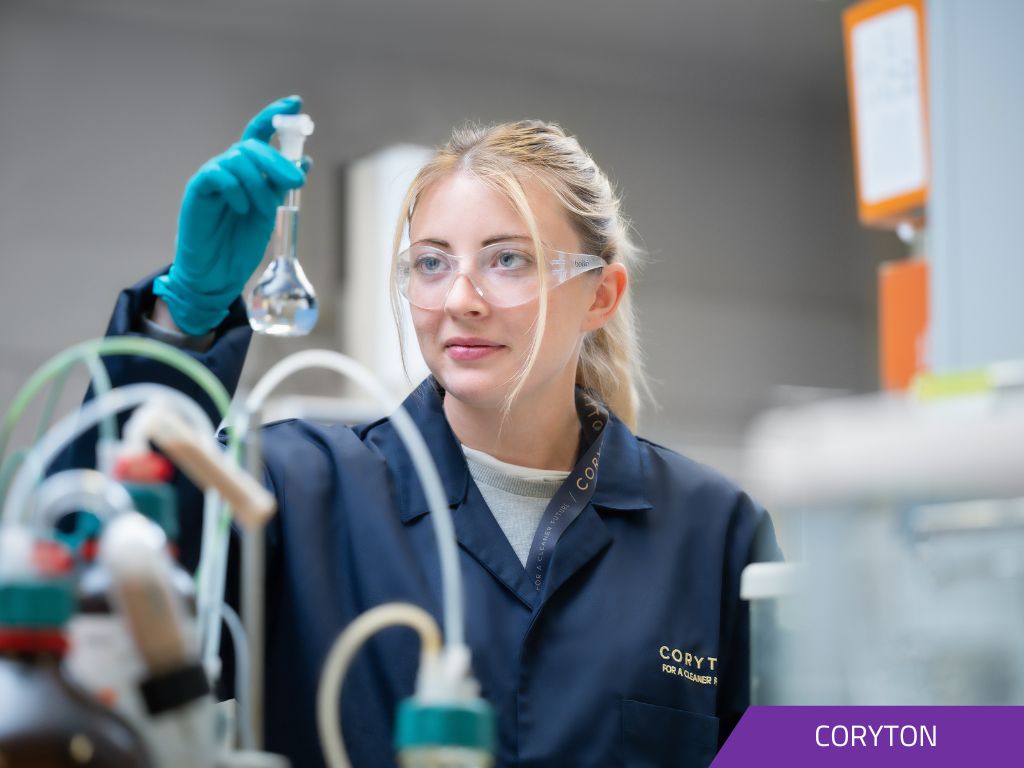
The ‘first generation’ of bio-synthetic fuels and lubricants used arable land to grow the required biomass. However, the downside to this approach is that an intensive amount of land is required – one study (2) estimated that to meet the USA transportation fuel usage requirement, 25% of the total land used for agriculture in the USA would have to be converted over to fuel production.
Consequently, this production of these first generation bio-synthetic fuels and lubricants competes head on with food production, and as a result is not a viable solution. Instead, the solution to conflict with food production is found with ‘second generation’ bio-synthetic fuels (known as advanced biofuels) and lubricants, which are manufactured from non-food crops.
Second generation bio-synthetic fuels and lubricants uses waste biomass such as waste agricultural material or food crops that are no longer fit for human consumption. Second generation bio-synthetic fuels and lubricants are created by either thermochemical conversion or biochemical conversion.
There are a number of thermochemical conversion processes. The first is known as gasification and is a process that has been used with conventional fossil fuels for decades. The gasification process converts carbon-based materials into carbon monoxide, hydrogen, and carbon dioxide.
A second thermochemical process is pyrolysis, which has also been used with fossil fuels in the past and is carried out in the presence of an inert gas like halogen. One other thermochemical reaction called torrefaction is similar to pyrolysis but is carried out at lower temperatures.
The other process for the production of second generation bio-synthetic fuels and lubricants is biochemical conversion, which consists of a number of biological and chemical processes. One popular example of biochemical conversion is fermentation with unique or genetically modified bacteria.
Rebecca Mann of Coryton says, “Whilst we can call upon many technologies to create our products, we focus mainly on second generation biofuels. This involves us using biological waste such as feedstock, agricultural waste (straw, for example) and forestry waste (such as wood pulp).
“After the crops have been harvested, we can ferment the waste matter that is left over and process it to make bio-ethanol. We then use this bio-ethanol to produce bio-gasoline, a sustainable fuel that can be pumped straight into cars without any modifications to the engine.
“We make over 4,000 blends a year using a range of techniques and sources to create bespoke products for our partners’ individual needs. We also have a range of sustainable fuels developed specifically for the motorsport industry.”
Some companies are now beginning to refer to a ‘third generation’ to refer to biofuel that has been derived from algae, which had previously been classed as part of the second generation group. This reclassification is due to the potential of algae biomass, which can provide much higher yields with lower resource inputs than other feedstock.
Rick Lee of Evolve Lubricants, a company that has created a range of bio-synthetic lubricants, explains the chemical processes that they employ. “We achieve excellent performance through molecular dynamics that enable precise control over branch length position and the proximity and the degree of branching for higher performance in a finished lubricant.
“This is achieved through control of the average double bond position in the molecule. Through the oligomerisation process we have precise control over the linear alpha-olefin chain length, average branching point and alkyl branch formation. Selective isomerization allows for an optimized final product structure properties with methyl branch addition.
“The result is critical control over fluid properties such as viscosity, vapour pressure, traction/friction coefficient and pressure-viscosity relationship resulting in energy efficiency and wear protection.
“Our products were designed to deliver the highest performance with narrow molecular weight resulting in higher flashpoints, initial boiling point and low volatility. The presence of a high molecular weight in the tail allows for low temperature optimization. Increased branching proximity and reduced branching index (more linear) delivers a reduced friction coefficient. These enhanced friction properties reduce shear heating and maintain film thickness at elevated temperatures, more so than fossil-based lubricants.”
What are Synthetic Fuels?
The creation of synthetic fuel in a laboratory or factory using just water, air and renewable electricity could potentially change the course of direction for powertrains, both on the road and on the track. Whilst the processes involved in the manufacture of synthetic fuels are well established, the development of such techniques has appeared to have ramped up over the last few years.
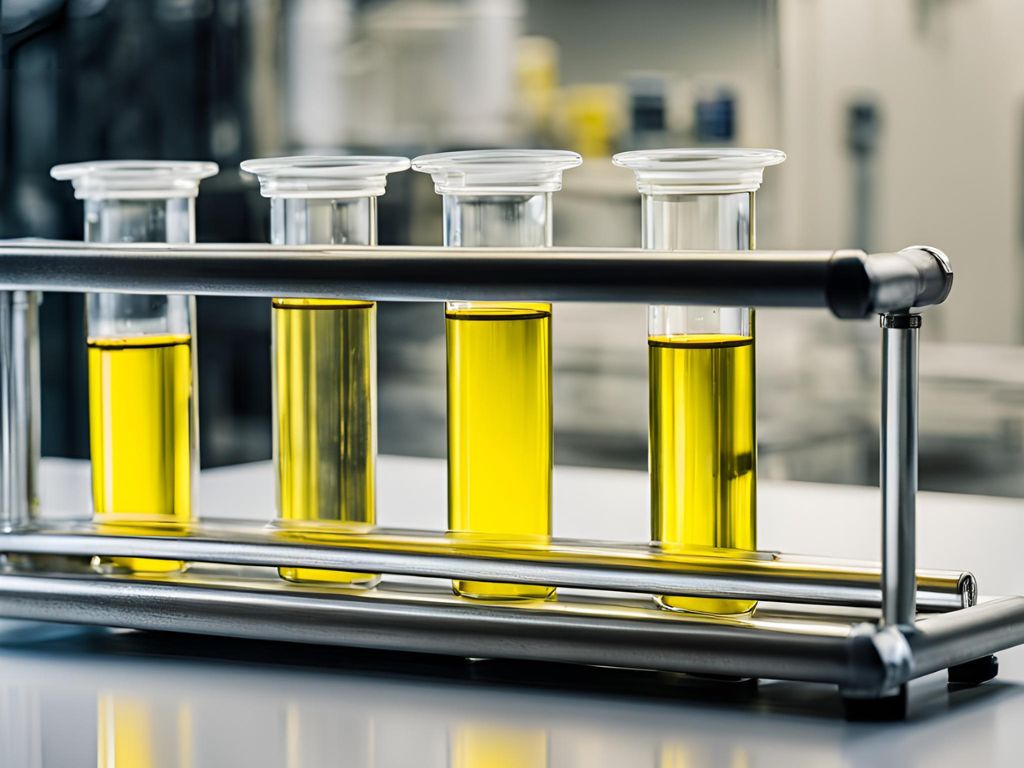
Synthetic fuels are manufactured by capturing carbon dioxide from the air which is then synthesised with hydrogen that has been extracted from water. As with biofuels, the carbon dioxide that is produced from combustion is cancelled out by the carbon dioxide that has been used to make the fuel. The processes involved in the production of synthetic fuels rely on the supply of electricity, hence if the electricity is from a renewable source then the fuel can rightly claim to be carbon neutral.
In the absence of any singular word that can be used to define the complete synthetic fuel production process, Zero Petroleum has coined the word ‘petrosynthesis’. The company provides the following definition of petrosynthesis as follows:
“Petrosynthesis (noun) – the artificial creation of organic compounds (synthetic petroleum/petrochemicals) and oxygen from inorganic precursors (principally water and carbon-dioxide) using non-biological energy (such as hydro, wind, solar, tidal, nuclear, geothermal); the industrial equivalent of photosynthesis, using neither energy nor material produced by either concurrent photosynthesis (plants) or legacy photosynthesis (fossil fuels).”
Similarly, there isn’t yet a widely accepted name for the fuel that is produced. “The fuel that is created goes by a number of different names, such as synthetic fuel, e-fuel and power-to-liquid”, says Paddy Lowe, who established the company after leaving Formula 1.
“Synthetic fuels are made using renewable power like wind and solar energy and the efficient industrial processes (carbon capture, electrolysis, thermal reactions), and should not be confused with biofuels or fuels made from waste.
“Using an industrial non-biological process is controlled, efficient, reliable, secure and scalable. Manufacture can be co-located in territory – self-contained energy generation without dependence on any foreign supply of raw materials. The process of manufacture and consumption is fully circular, creating an industrial carbon cycle which can continue indefinitely in balance with the environment, just as the biological carbon cycle has done for billions of years.”
There are a number of discrete steps in the production of synthetic fuels. The first step is to capture, remove and store carbon dioxide from the air. One such method is known as direct air capture (DAC).
Air is pulled into an air contactor by one or more large fans, and it is then introduced to a potassium hydroxide solution. This solution creates chemical bonds with the carbon dioxide in the air, creating a carbonate salt that is captured in the solution.
A number of chemical processes are then carried out on this carbonate solution in a pellet reactor to turn the salt into small solid pellets, which are then heat treated in a calciner to release the pure carbon dioxide gas. The left-over pellets can be hydrated and then re-used.
The next step is to convert this carbon dioxide into carbon monoxide. This is done by a process that is referred to as ‘reverse water gas shift’ (RWGS). The RWGS process converts carbon dioxide and hydrogen into carbon monoxide and water, as per the following chemical equation:

Note that this process requires a significant amount of heat and note also that the reaction of carbon dioxide with hydrogen can also produce methane, which has to be suppressed with a selective catalyst.
The other ingredient for synthetic fuel production is hydrogen, which is obtained by the electrolysis of water. This process takes place in an electrolyser and involves the use of electricity to break water down into hydrogen and oxygen.
The final step is to carry out a catalytic chemical process that takes the carbon dioxide that has been captured from the air and turned into carbon monoxide via the RWGS reaction, adds it to the hydrogen that has been obtained by electrolysis of water, and creates the required hydrocarbon (plus a number of other by-products, such as water).
This chemical process is called Fischer-Tropsch synthesis, in recognition of two German inventors, Franz Fischer and Hans Tropsch, who pioneered this process in the 1920s.
The underlying chemical formula for this process is:

where n is an integer. Different hydrocarbons can be created, by changing the value of n – for example, if n is 1 then methane is produced. Changing the catalyst, temperature and type of process will create different hydrocarbons. Almost any hydrocarbon can be manufactured, such as plastics, gasoline and lubricants.
The catalyst is based on what are called transition metals, which are typically nickel, iron, cobalt and ruthenium. Nickel is used for the formation of methane, whereas iron is used for the production of hydrocarbons that are created with a lower ratio of hydrogen to carbon monoxide. Ruthenium is usually prohibitively expensive for use as a catalyst in most applications.
Lowe reports that cobalt is commonly chosen as a catalyst for the production of gasoline but would not disclose its own choice of catalyst – this would appear to be part of the company’s ‘secret formula’.
The Fischer-Tropsch process is highly exothermic, creating a large amount of heat. As a result, the company mentions that the overall efficiency of the chemical energy that is created in the synthetic fuel is only around 40 to 45%.
The other issue is of course cost. At the moment the cost of the production of synthetic fuel is higher than that of fossil fuel. As an example, Lowe mentioned that their SAF (sustainable aviation fuel) is currently four times the price of regular jet fuel. This high price is largely down to the relatively low volume that sustainable fuel is currently made in. Lowe drew a parallel with the excessive costs of energy that was derived from the early wind farms, again due to the initial low number of such power sources. Lowe was confident that the costs of its fuel will drop when the volume of fuel produced is increased.
Aside from the carbon-neutral aspect with sustainable fuels, there is one other advantage with regards to emissions from combustion of such fuels in an IC engine. Obviously, the combustion of this fuel creates the primary products of water and carbon dioxide, but as there are no non-hydrocarbons present in the combustion, there are lower levels of particulates and nitrous oxide present in the emissions. Also, as there is no sulphur present, there have been favourable comments about the improvements in the smell of the fuel.
Summary
Sustainable fuels and lubricants will play a pivotal role in the decarbonising of our transportation in the coming years and decades. Rebecca Mann of Coryton observes that 1 tonne of carbon dioxide that is saved today is equivalent to having to save 30 tonnes in 2050. The long term benefits of reducing the carbon footprint of vehicles on the road today will be extremely powerful.
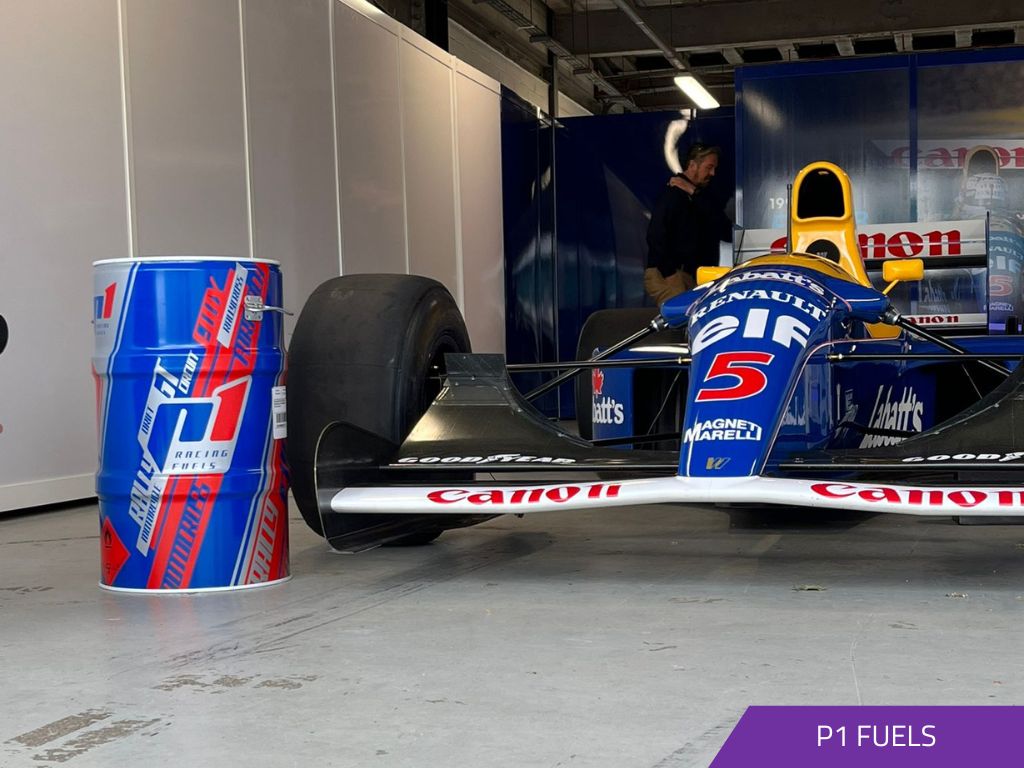
Bio-synthetic fuels and lubricants use biomass that has captured carbon dioxide from the atmosphere. Synthetic fuels and lubricants replicate the process of photosynthesis that was used to create fossil fuels – Paddy Lowe of Zero Petroleum notes that they can complete a task in 3 minutes that nature took six million years to do!
Motorsport will play a vital role in the transition to these sustainable fuels and lubricants. Jean-François Toulisse of TotalEnergies says, “In terms of motorsport activities, we can see that more and more championships are looking for sustainable fuels and lubricants for the near future of their series. This is clearly a beneficial solution to the environment, whilst also keeping the spirit of IC engines alive with the fans.
“EV powertrains won’t be the only solution for motorsport. We are not here to say which energy will be the best on track, but we will see all kind of solutions (biofuels, synthetic fuels and electricity) on the track in the years to come!”
Mann leaves us with a parting word on the future for IC engines that sustainable fuels and lubricants could be a significant part of. “It’s our belief that we need a range of solutions working together to help meet our net-zero target and that sustainable fuels could play a significant role in the mix.
“Across the world there are lots of great examples of sustainable fuels and lubricants working well in action, and there’s a great deal of development work underway. Much of what we’re working on we can’t disclose. But we’re constantly exploring new innovations and ideas to push the sector forward. We’re driven by our mission to create a better future.”
References
1. Race Engine Technology issue 144, January 2023. https://www.highpowermedia.com/Product/race-engine-technology-issue-144
2. Savage, D. F., Way, J., Silver, P. A. (2008) “Defossiling Fuel: How Synthetic Biology Can Transform Biofuel Production” ACS Chemical Biology 3(1):12-16.
Acknowledgements
I’d like to thank Rebecca Mann of Coryton, Jean-François Toulisse of TotalEnergies, Mike Bassett of MAHLE Powertrain, Rick Lee of Evolve Lubricants, Benjamin Cuyt of P1 Fuels, Paddy Lowe of Zero Petroleum, and Yann Labia of Haltermann Carless for their help with researching this article.