PISTON FORGING TECH
All of our Cosworth production pistons start life as a piston forging to ensure that they are as strong as possible.
Put simply, the forging process involves pushing a bespoke die under great pressure into the billet. As a result, the billet material flows into the required shape of the piston. The forging process gives us the finished machined shape in the undercrown. This reduces the amount of machining that is required. Further, the orientation and distortion of the grains in the material is optimised to give superior mechanical strength. Aligning the axes of the material grain in a certain way can have a significant impact on the structural properties of the piston.
Temperature Effects
Our pistons begin their life as a billet of extruded aluminium alloy bar. This billet is heated to a pre-determined temperature to ensure that the billet is soft, but not at melting point. When the billet is at the correct temperature, it is placed into the forge and shaped by the die. The forging temperature needs to be carefully controlled. This temperature will have a significant effect on the homogeneity of the microstructure. If there were localised changes in the billet temperature then this could lead to inconsistencies in the material properties of the finished piston. For example, if the die was cold then the outer surfaces of the piston would cool rapidly. This would lead to a varied grain structure in the finished piston.
Hence the die is heated to the same temperature as the billet, creating a process known as isothermal forging. This process that keeps the billet at its maximum elevated temperature throughout the entire forging operation. During the forging process, any cooling at the interface between the die and billet is eliminated, which can greatly improve the flow characteristics and hence the grain structure of the finished item.
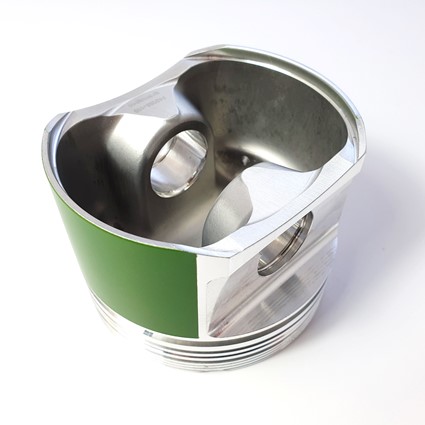
If you’d like to know more about our genuine Cosworth pistons and how they can provide you with the performance and reliability that you need from your engine then please get in touch via our Contact page.