CRANK BEARING MATERIAL TECH
There is nothing ‘plain’ about a plain bearing, especially when it comes to fluid film journal bearings, like those found on the crankpin and mains journals of the crankshaft. There have been continuous advances in crank bearing material, which enable bearings to last longer between rebuilds.
The first examples of journal bearings were made from Babbitt metal (sometimes also referred to as white metal), named after Isaac Babbitt who in 1839 developed an alloy to be used as a bearing surface in plain bearings. The exact composition was kept a closely guarded secret for a number of years, but was eventually disclosed as an alloy of lead, tin, copper and antimony. These days we tend to refer to any lead- or tin-based alloy material as a Babbitt metal.
Babbitt metals tend to be extremely soft, especially when compared to the hardened crankshaft journals. However, the composition of a Babbitt metal is a matrix of small, hard crystals contained in a softer metal. The aim is that, as the bearing wears, the softer metal yields and creates routes for the oil to pass through, improving lubrication and giving the bearing some degree of conformability.
Originally, a thin layer of Babbitt metal would be applied directly to the bore of the substrate material, but the need to periodically refurbish this surface led to the introduction of interchangeable steel or bronze shells onto which the Babbitt metal could be applied.
Thin Walled Bearings
The most famous example of the replaceable bearing shell that was first developed for high-performance engines was the Vandervell ‘thin-walled’ shell bearing. As the name suggests, the shell comprised a thin strip of steel that was rolled to create a semicircular shell, and the bearing material could then be coated onto the inner diameter, creating what was termed a bimetallic bearing. The steel backing was made from a high-strength steel alloy that allowed the bearing to be interfered into the rod and cap halves without yielding.
Today’s bearings still rely on a high-strength steel alloy backing in most cases, but here the similarities with their distant ancestors ends. Bearing manufacturers discovered that a steel-backed bearing combined with a thin Babbitt metal layer was prone to wear, reducing the time between bearing change intervals. If they wanted their products to last longer and be more reliable, they had to find a way of adding strength and wear resistance into the bearing. That thinking led to the introduction of a multi-layered bearing, which could provide the compromises needed between all the functions the bearing had to provide.
Bimetallic bearings were therefore usurped by trimetallic bearings, which are composed of a backing, a substrate (or lining) and an overlay. The substrate layer gave the bearing its load-carrying capability and provided resistance to wear and cavitation.
Bearing Material
The most common material for the substrate layer is a copper and lead alloy, which replaced the previous versions of tin-based Babbitt metals a number of years ago. Such alloys tend to consist of 20-40% lead, with the rest made up of copper and sometimes small amounts of tin, silver or nickel.
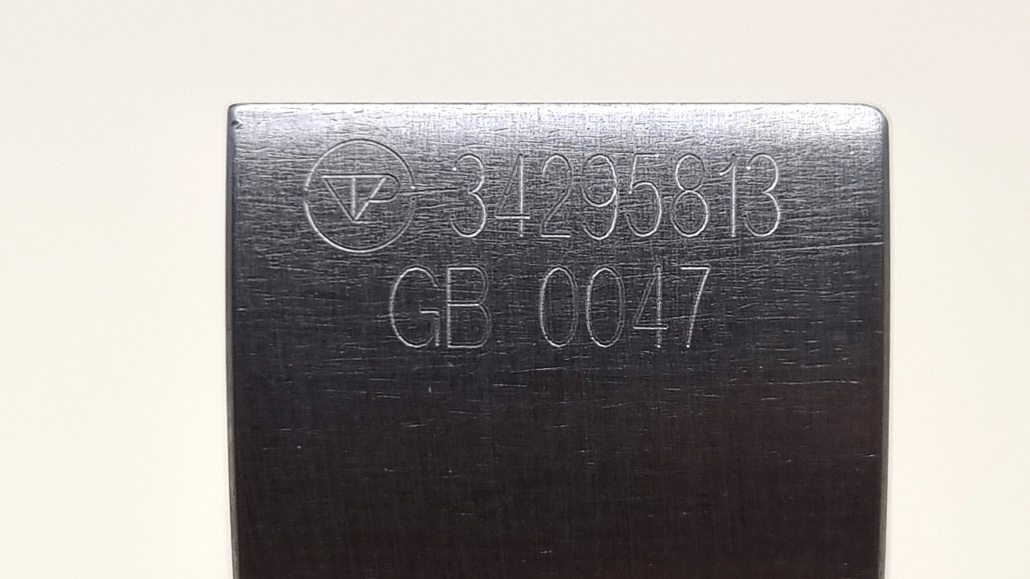
Vandervell (now part of the MAHLE group) created its own unique specifications for crank bearing material, characterised as strip-cast leaded bronze cast onto a steel backing plate, most notably VP1, VP2 and VP10, all of which have differing amounts of lead, tin and iron elements.
Overlay Material
Overlays used to consist of lead-tin or lead-indium Babbitt metals, but as with the substrate, there is now a plethora of different overlay material options available.
MAHLE state that the overlay provides three critical characteristics – conformability, compatibility and embeddability.
Conformability – in an ideal world, the bearing housing and the journal shaft would be infinitely stiff and the alignment of the shafts would be perfectly true. Of course, in the real world that is not the case: the cylinder block and con rod assemblies will flex as load is applied, and the crankshaft journals will twist and bend, albeit by imperceptible amounts in most cases. But it means the bearing material must be able to distort elastically in response to distortions of the mating parts.
Compatibility – it is almost impossible to prevent boundary and mixed lubrication conditions during low-speed running, so there will sometimes be metal-to-metal contact between the bearing’s running surface and the crankshaft journal. The chosen material for the surface of the bearing must therefore be compatible with that for the crankshaft journal. A poor combination of materials can lead to galling or even seizure.
Embeddability – even with the best filtration systems and oil additive treatments, there will always be minute foreign particles in the oil that the bearing will have to cope with. As a result, the overlay material of the bearing must be able to absorb or embed this debris in the surface, otherwise the particles will eventually score the surfaces of the bearing and the journal at high loads.
Bearings from Modatek
The original crankshaft journal bearings that were used by Cosworth on their early engines like the DFV were developed with Vandervell. Over subsequent years these bearings have proven to be reliable in a wide range of applications including Formula 1.
We continue to use bearings from Mahle, who took over Vandervell in 2007. We now stock a wide range of Mahle bearings, including rod and mains bearings for the Cosworth YB engine.
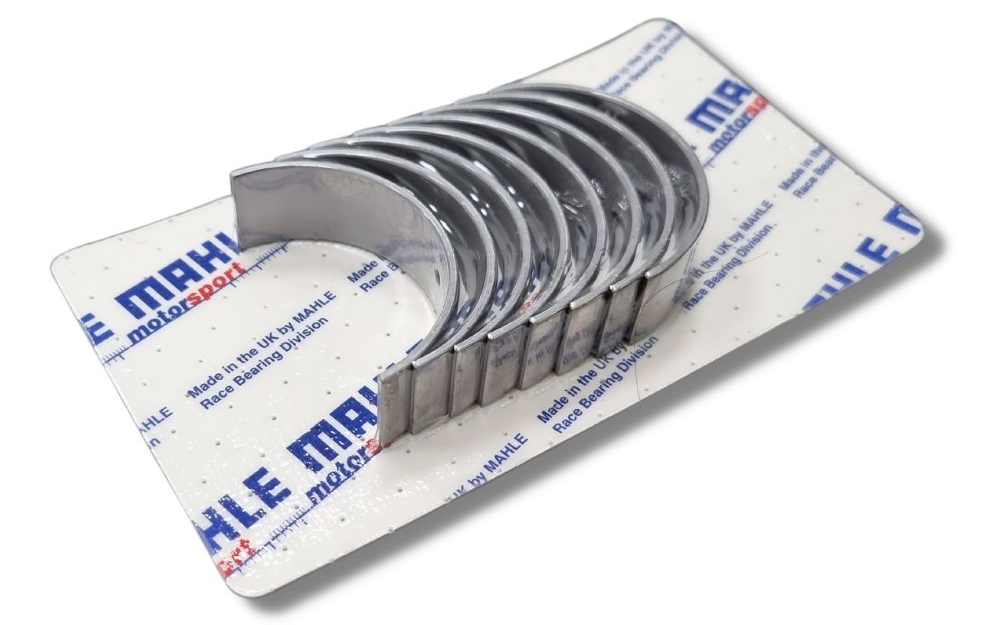
This feature on crank bearing material is based on an article written by Modatek’s Matt Grant for Race Engine Technology, issue 114. You can purchase a back copy of this publication here: https://www.highpowermedia.com/Product/race-engine-technology-issue-114